Wire Arc Additive Manufacturing (WAAM)
Viele unserer Schweißzusätze können für WAAM direkt eingesetzt werden. Besonders hervorzuheben sind die Legierungen MA-6063, MA-4018, MA-4046, MA-2319 und MA-5183.
Gleichzeitig sind wir an einer Reihe von Forschungsprojekten zur Entwicklung neuer Werkstoffe und Verfahren für die Additive Fertigung beteiligt.
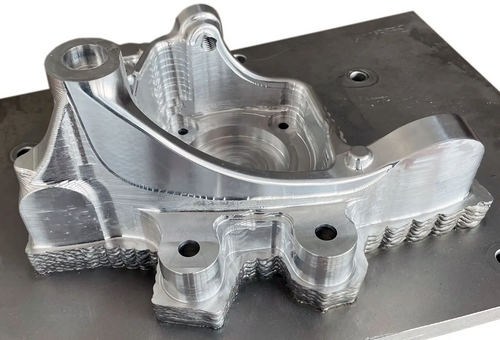
Innovation, Nachhaltigkeit und Null-Fehler-Produktion in einer baltischen Schiffswerft
MIGAL.CO GmbH - Ihr Schlüssel zum perfekten Schweißen
Jumbo XL Fass
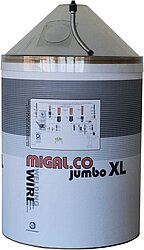
Unser Jumbo Fass enthält bis zu 240 kg Aluminiumschweißdraht. Es wurde für wahre Großverbraucher, speziell in Verbindung mit dem mechanisierten Schweißen entwickelt. In Verbindung mit dem Rolliner ergibt dies die perfekte Lösung.
Rolliner 3G
Rolliner 3G ist die Fortsetzung des seit 10 Jahren bewährten rollengeführten Drahtförderschlauchs mit wesentlichen Verbesserungen. Die einzelnen Elemente des Rolliners enthalten jeweils ein Rollenpaar und sind über Gelenke miteinander verbunden.
WIG-Stäbe in 2,5 kg Verpackung
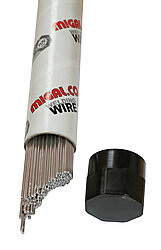
Wir liefern nun unsere Aluminium WIG-Stäbe auch in einer 2,5 kg Verpackung. Die Verpackung besteht aus einem Rohr mit 2 Plastikkappen und ist somit auch wieder verschließbar. Momentan liefern wir die Legierungen MA-4043 und MA-5356 von 1,6 bis 3,2 mm. Bei entsprechender Nachfrage können wir dies für andere Legierungen erweitern.
"Innovation trifft Nachhaltigkeit: Bär Cargolift optimiert mit MIGAL.CO die Schweißtechnik in der Ladebordwandproduktion“
Willkommen bei MIGAL.CO
Entdecken Sie branchenführende Aluminiumschweißzusätze, Kupferschweißmaterialien, hochwertige Edelstahlschweißprodukte und Nickelschweißlösungen bei MIGAL.CO. Unsere Expertise in Schweißtechnik erstreckt sich über umfassende Beratung, innovative Schweißtechnologie und ein Technologiezentrum, das von unserem Team aus hochqualifizierten Fachkräften unterstützt wird. Profitieren Sie von unserem vollständigen Angebot an Drahtförderprodukten und fortschrittlicher Schweißsoftware, um Ihre Produktionseffizienz zu maximieren.
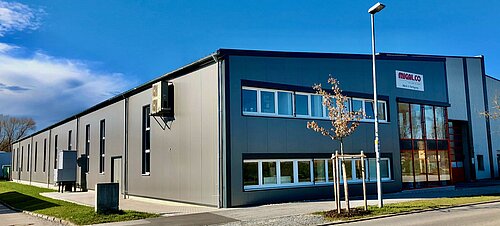